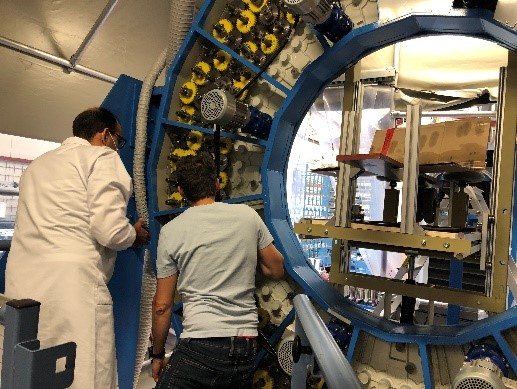
Here we come to a successful end of an exciting industrial experience in Centexbel, Belgium. The hands-on experience with the circular braiding machine, its cutting-edge performance, the limitations as well as facing difficulties even to the extent of witnessing its breakdown has been a remarkable experience in the scientific pursuit.
The secondment had been split into two phases. The 1st phase from 6 September 2021 to 1 October 2021 started with the introduction to the machine, the control panel and its mechanical arrangement. The configuration comprised of a total of 256 horn gears arranged in four circular layers, proportionally increasing in diameter as progressing outward. All horn gears have four slots for bobbin carriers along with one for uniaxial yarns, if desired for triaxial braiding. As an important input parameter along with the braid angle, the path is determined by the fundamental trigonometric relation of tangent of the braid angle as perimeter / path. For the usually adopted braid angle of 45 degrees, the path = perimeter. For instance, for a 100 mm cylindrical mandrel, the path can be 314 mm with braid angle as 45 degrees. This becomes more complex with nonstandard geometrical mandrel shapes. The scientific discussions also helped to reveal the exact limitations and issues faced by the engineers during the process, such as the transient change in braid angle at drastically changing cross-sections. These issues can be prospectively addressed by a coupled process-level simulation. Other vacuum infusion processes were also visually demonstrated by the team.
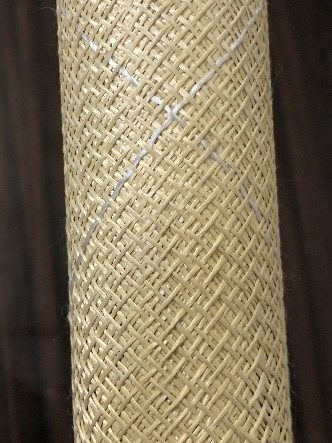
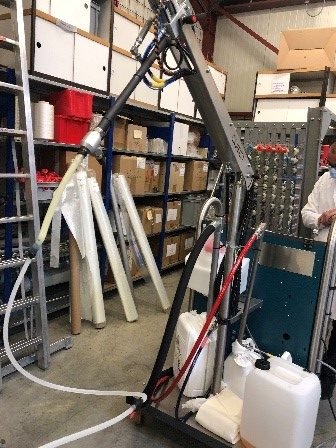
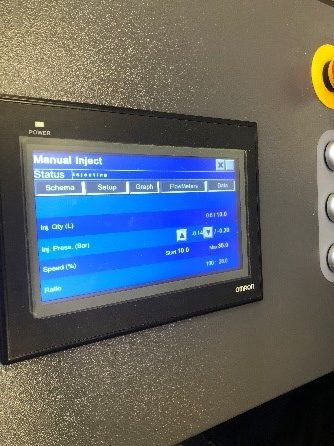
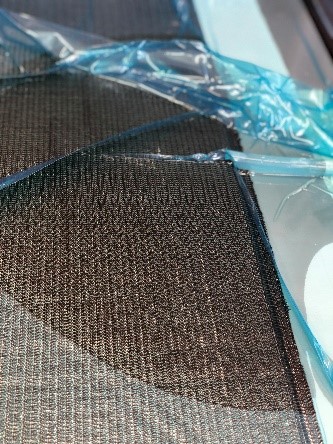
The breakdown of the machine was a challenging experience, but it enhanced the insight into the details of the machine. The breakdown was due to the jamming of one of the carriers in the track. The team had to initially attempt to resolve the issue internally and therefore, we had to dismantle many parts of the machine. This was exciting to identify the problem, discover mechanical details of the machine, the gear and motor arrangement etc. Nevertheless, the second phase of the secondment had to be further postponed for the machine to be operating.
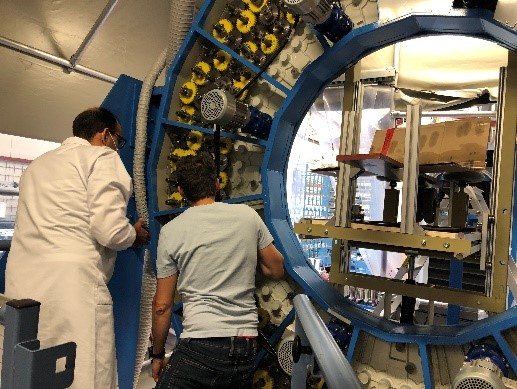
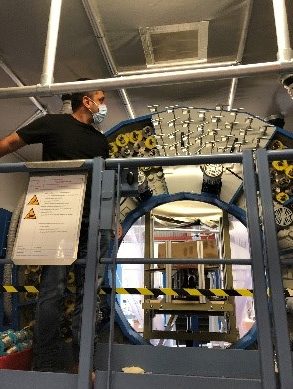

The 2nd phase of the secondment started on 22 November 2021 to 24 December 2021, and it was exciting to see the machine operating again. In this phase, the braiding of a nonstandard mandrel geometry as shown in figure 3 had been carried out. The triaxial braid as seen on the right in figure 3 has been deposited in four layers of braid to achieve the desired thickness. The length of each mandrel was 2 meters. This was the core of this secondment, to be a part of this practical experience, to identify the errors and iterate back-and-forth to achieve the desired output.

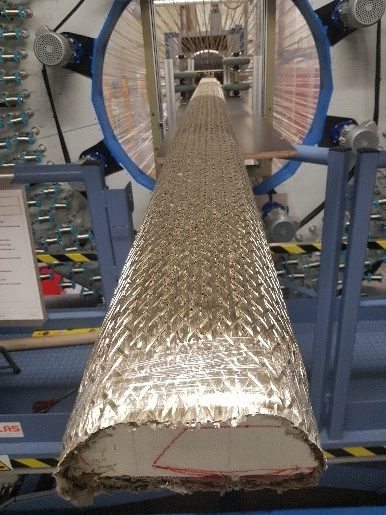
The experience with Centexbel has been significantly important in this period of research. Working in an industrial environment, with communication of academic-industry viewpoints and informal discussions within the team about scientific challenges which can potentially be aided with simulations have been remarkable. This practical experience with the machine shall be highly consequential in the scientific pursuit.
Contributed by Indrajeet Patil (ESR 2)